Harrison M400 Lathe Manual Pdf
Harrison M400 lathe email: HARRISON M400 Lathe An Operation, Maintenance & Parts Manual is available for the A heavily built, if conventionally designed industrial-quality lathe, the M400 had an exceptionally deep (380 mm - 15') and wide (360 mm - 14.125') bed. Although intended as a medium-duty production lathe it was also claimed by the makers to be capable of handling, through its wide speed range and great strength, both toolroom and general repair-shop work.
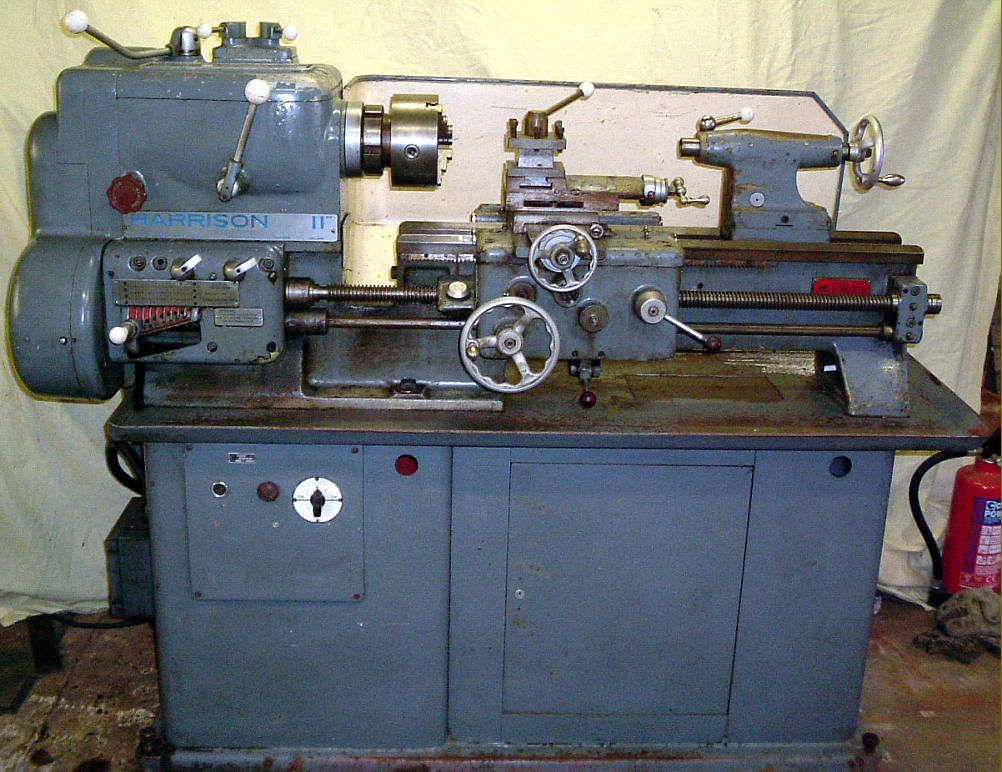
Manufacturers of colchester and harrison manual and cnc lathes, pratt burnerd chucking systems and Clausing machine tools. Results 1 - 10 of 10. Harrison_m300_machine_ manual.pdf - scribd. Harrison_M300_Machine_Manual.pdf - Download as PDF File (.pdf), Text file (.txt) or read online. Harrison M300 Metal Lathe Manual. Harrison m400 horizontal lathe / turning machine for sale. Coda 2 Serial Number Keygen. HARRISON M400 horizontal Lathe / Turning Machine For Sale. Warning: Invalid argument supplied for foreach() in /srv/users/serverpilot/apps/jujaitaly/public/index.php on line 447.
It had a swing of 450 mm (17.75') and a capacity of either 1000 mm, 1500 mm or 2000 mm (40', 60' and 80') between centres; the induction hardened bed could be ordered either straight, or with a detachable gap able to accept material up to 642 mm (25.25') in diameter and 200 mm (8') thick. All models had 18 speeds progressing in a ratio of 1.46 from either 40 to 2000 rpm, or 31 to 1600 rpm, powered by a 7.5 kW (10 hp) 3-phase 1500 rpm mounted on an adjustable plate bolted to the back of the bed immediately below the headstock. Four V belts transmitted the power to the geared headstock - the input shaft of which carried individual clutches (made by Matrix) for forward and reverse drive; on the outboard end of the main spindle was a powerful 'Fail-safe' self-compensating electromagnetic spindle brake manufactured by Warner.
Spindle speeds were selected by a pair of neat, concentrically mounted dials that allowed both rapid, positive selection - yet the minimum of confusion for the new operator. Fitted with a hardened and ground No. 8 D-1 Camlock nose the 65 mm (2.5') bore spindle carried a reduction sleeve to hold a 5 Morse-taper centre and ran in expensive Gamet pre-loaded Super-precision bearings. The headstock gears and bearings (for this was a machine of considerable strength and capacity), were pump lubricated from a separate oil tank held in the base of the machine. Fitted with induction-hardened gears the dual English/metric screwcutting gearbox could, without changing or rearranging any of the changewheels, produce 51 inch pitches from 2 to 84 T.P.I. And 54 metric from 0.2 to 14 mm. By the use of additional changewheels 18 Module pitches from 0.2 to 3.5 MOD and 27 Diametral from 8 to 72 DP could also be generated.
The 27 power sliding feeds varied from 0.04 mm to 2.84 mm per revolution of the spindle in metric mode and from 0.0016' to 0.112' in English with the power cross feed rate was arranged to be half the sliding rate. The gearbox was controlled by three smooth-finish levers (like those on other contemporary Harrison lathes these could be difficult to operate with oily hands), and a single rotary selector; an oil supply was held in the base of the headstock and circulated by the simple but effective means of splash. Adjusted to the bed by a tapered gib strip the carriage was fitted with a conventional spoked wheel for movement by hand (the wheel could be disengaged when power feeds were in use) and the 32 mm (1.25') diameter leadscrew (of 6 mm pitch or 4 t.p.i.) carried a torque-limiter and was engaged only for screwcutting; the leadscrew clasp nuts were arranged to 'float', a feature that Harrison claimed both reduce wear and improved threading accuracy. The powershaft was fitted with an adjustable over-load protection device that could also act as a carriage stop) provided the sliding and surfacing feeds used in normal work. The double-wall apron was of a completely new design for Harrison and, instead of the usual worm-and-wheel mechanism, was fitted with twin-bevel gear drive and dog clutches (a mechanism used as far back as the late 1800s) to the power sliding and surfacing feeds; this feature allowed the operator to instantly reverse either without having to stop the headstock spindle. A single lever was used to both select and engage the power feeds and returning it to a central position, to stop the cut, could be done without effort, no matter how hard the lathe was working. The apron carried a supply of oil in its base that was distributed to the apron's gears and spindles, the bed and cross slide by an automatic, 'one-shot' pump.